Boot Build Part 2Step 4 - Fibre-glassing
For anyone who hasn't used fibreglass before, I'll start with a spot of safety. My advice is to:-
1. Wear eye protection to avoid splinters of fibreglass getting into your eyes.
2. Wear the gloves - the packs come with gloves. but they are poor and I advise using latex gloves and changing them regularly. Even if you wear them you can still get small slivers of fibre-glass sticking in your fingers
3. The resin stinks and the odour is quite strong, so if you are attempting it in a garage open a window or the garage door.
Before starting this part, cover the boot floor and hatch opening load lip with the bin liners that I mentioned. this will avoid marking up the boot with resin spillage and fibre-glass shards. It also protects the hatch load lip as you WILL be spending time getting in and out of the boot.
So, once you are kitted up, you need to cut the fibreglass. A sharp pair of normal scissors will do the trick. It is up to personal preference as to how large you make the strips, but I was fairly flexible in that you can use 10 x 30 cm strips most of the time and then smaller pieces for tricky edges and corners and larger pieces for the larger flat areas.
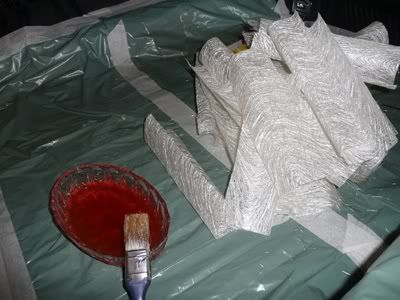
The kit gives instructions on how to mix the resin. All I can add is that the resin takes a lot longer to set when cold or if you don't put enough hardener in. Be careful though. because if you add too much hardener it can literally set in the mixing dish before you have used it all.
Once the resin is mixed, start from the bottom and piece-by-piece work your way to the top. You should cover approximately 100 mm of the boot floor and so you need to allow for this in the masking up process. Make sure you overlap each piece by at least 25mm to give the individual sheets chance to bond together with the resin. I found it best to brush a thin coat of resin directly onto the masking tape first so that the fibre-glass sheets would stick better. Stipple in the resin into the fibre-glass patches until each one loses its white colour. Also be careful to avoid bubbles of air, which weaken the mould. Once the first layer is done, stand back and admire your handywork and get some fresh air!
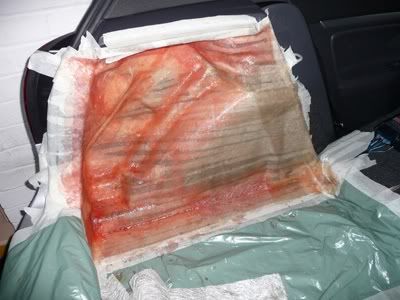
Repeat this procedure for at least two more layers, so that you end up with a solid mould. With each layer you build up ensure that you do not get any air between the layers.
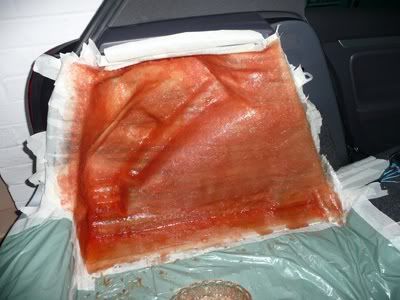
Once the mould has had chance to set, prise the mould from the arch. It will come out, but the masking tape has a good hold and so it will need a good tug. I found that pulling from the bottom was easier to remove it.
Step 5 - trimming the mould
First, remove all the masking tape from the back of the mould.
Using a jigsaw, trim down the jagged egdes of the mould. Try to follow the outline of the hatch opening, the bottom of the parcel shelf, the back seat and the boot floor. When cutting allow for about 75mm width of the mould on the boot floor.
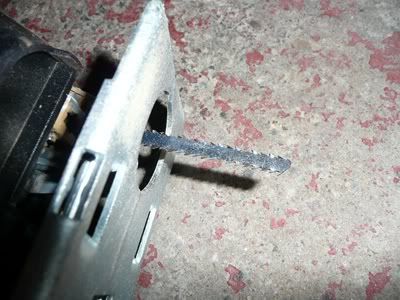
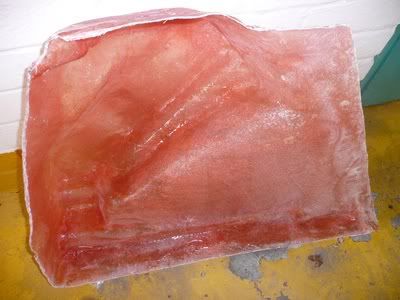
Once cut, refit the mould into the wheel arch and check that it fits okay.
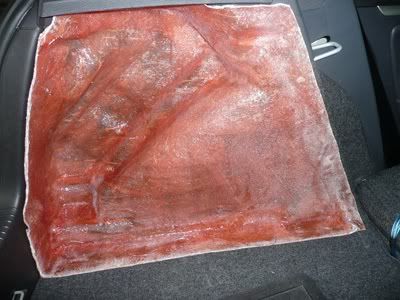
In my case I also checked that the parcel shelf cleared the mould and had to cut out an extra piece.
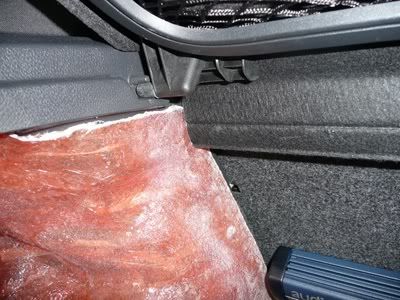
The next photo shows the mould with the piece cut out to allow for the parcel shelf
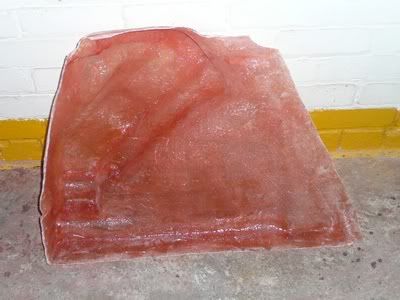
Part 3 coming soon............
